Thermoelectric Device Turns Body into Watch Battery
Thermoelectric Device Turns Body into Watch Battery
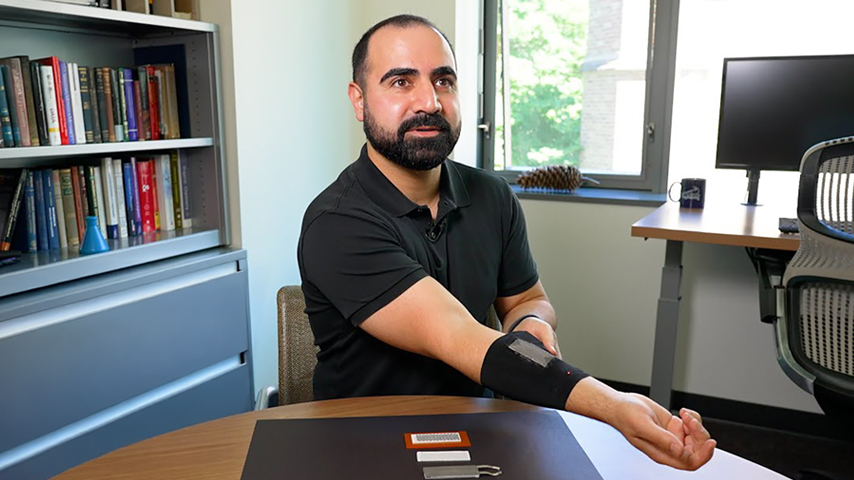
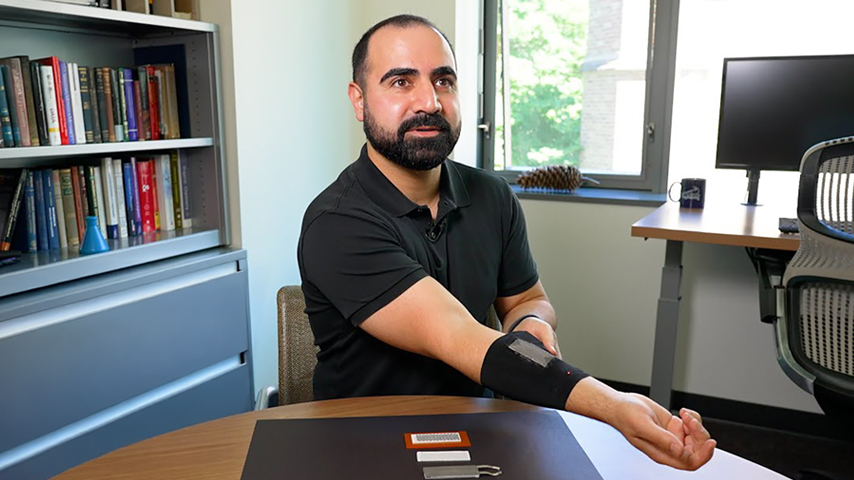
It takes as little as 10 degrees temperature difference for the stretchable membrane to generate usable power.
Existing TEDs used rigid materials and electrodes that couldn’t conform to the skin’s curvature or provide flexibility during movement, causing inconsistent temperatures and, therefore, insufficient electric current. These TEDs often felt stiff, fragile, and uncomfortable because of their complex construction and rigid materials, making them impractical for wearables.
“The biggest challenge with current wearable TEDs involved their rigidity, which prevented good contact with the heat source. We created a flexible device that can be wrapped around the heat source and generated enough energy for practical application,” explained Mohammad Malakooti, an assistant professor of mechanical engineering at the university.
Thermoelectric devices (TEDs) generated electricity through the Seebeck effect to create a voltage or electric current, capable of powering a device or charging a battery. When a temperature difference existed across the device containing semiconductors, electrons migrated from the hot side to the cold side, producing voltage. Larger temperature differences resulted in greater voltage and current potential.
It's Time to Renew Your ASME Membership
While TEDs have received attention for drawing power from waste heat such as engine exhaust, the temperature window between the skin’s surface and ambient air is smaller than typical thermoelectric use cases. This prompted researchers to develop a device capable of generating enough electricity to power sensors and LEDs with minimal temperature gradient.
The prototype generated sufficient energy with just a 10 °C temperature difference, far lower than the 60 °C gradient required by existing TEDs. This temperature difference could come from the skin’s surface and ambient air or from placing the device on a warm surface. In hotter climates, where ambient air matched or exceeded skin temperature, the ambient air often became the “hot side” of the device.
The device worked whenever a temperature difference appeared across it, though with differences under 10 °C, power output dropped, making the device less efficient.
Self-healing
To maintain skin contact, the team constructed the device with soft and stretchable layers, each serving a specific function. The middle layer held an arrangement of individual n-type and p-type thermoelectric pins, which enabled electron migration from the hot side to the cold side, converting thermal energy into electricity.
“We use nontoxic liquid metal to connect all the semiconductors in a specific arrangement, closing the circuit without making the device stiff,” Malakooti said. “We then print a layer of liquid-metal elastomer composite on each side of the device. These liquid-metal composites are engineered to be soft, with high thermal conductivity while remaining electrically insulative.”
The liquid metal composite layer effectively transferred thermal energy from the outer surfaces, which absorbed heat from the skin. One of the outer layers, designed as a heat sink, used a raised rib design to increase surface area and facilitate heat dissipation. With a temperature difference of only 10 °C, the device generated 115.4 microwatts per square centimeter, significantly higher than any reported energy density for flexible thermoelectric generators to date.
More For You: Wearable Air Curtain Could Protect Workers From Pathogens
The research team developed the polymer material that housed the circuitry and facilitated heat transfer. Focusing on advanced materials, they drew from their mechanical engineering expertise to craft specific polymers tailored for their application instead of relying on commercially available options. These smart polymers allowed the device to return to its original shape after deformation, demonstrating hyper elasticity while efficiently transferring heat.
Although the device can be bent, twisted, and stretched to 230 percent its original size without mechanical or electrical failure, stretching the device up to 600 percent strain (seven times its original length) temporarily broke the embedded electrical circuit, stopping power generation. However, the liquid metal traces, moving within its cavity during stretching and flowing back afterward, demonstrated an electrical self-healing effect, allowing the circuit to easily reinstate once the device returned to its original shape.
Their research was reported in the paper, “3D Soft Architectures for Stretchable Thermoelectric Wearables with Electrical Self-Healing and Damage Tolerance,” published on August 30 in the journal, Advanced Materials.
During development and testing, the device endured multiple punctures and then 2,000 stretching cycles at strain levels of 50 percent, maintained functionality, and showed no degradation in power generation.
Researchers used a 3D printer and customized functional materials to create and print the raised rib architecture of the outer layer.
“Our goal was to increase surface area for better heat dissipation. We also wanted to ensure simple 3D printing. We didn’t spend too much time optimizing the design at this stage, but we could improve the profile to boost heat transfer further,” Malakooti said. If their device needed to generate more electricity or required construction with different materials or a smaller surface area, the team recognized that optimizing the heat sink layer could offer significant benefits.
Their mechanical engineering background also helped them foresee potential manufacturing challenges if their research advanced to commercial production. The team balanced maximizing heat transfer and voltage potential with constructability. While improving the design could increase efficiency and energy generation, a simpler design, producing adequate power, would be easier and cheaper to manufacture.
Nicole Imeson is a technology writer in Calgary, Alta.