Blog: Electric Vehicle Advances Accelerate
Blog: Electric Vehicle Advances Accelerate
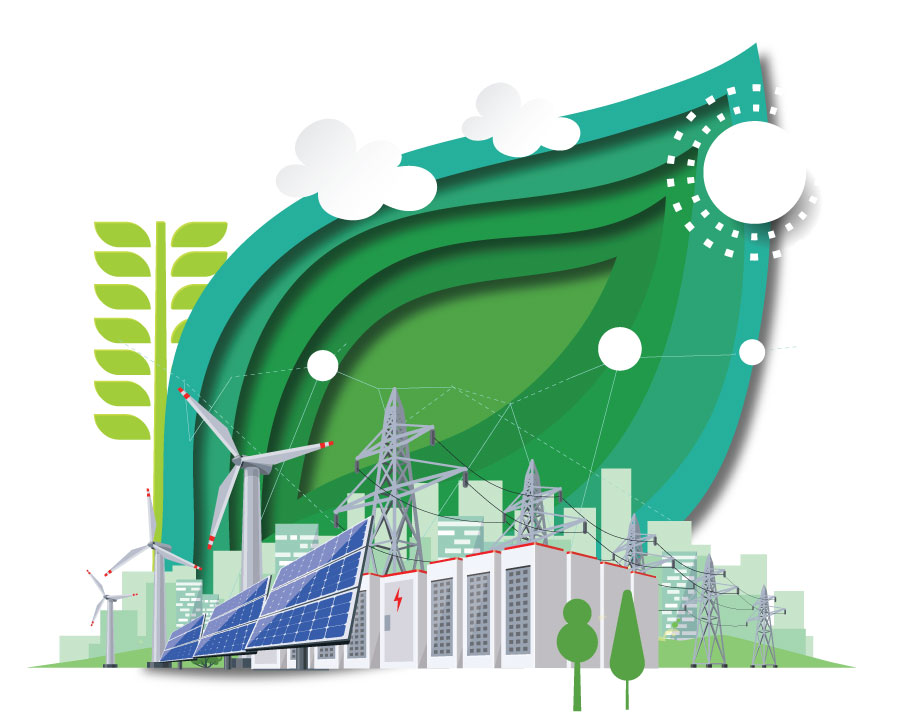
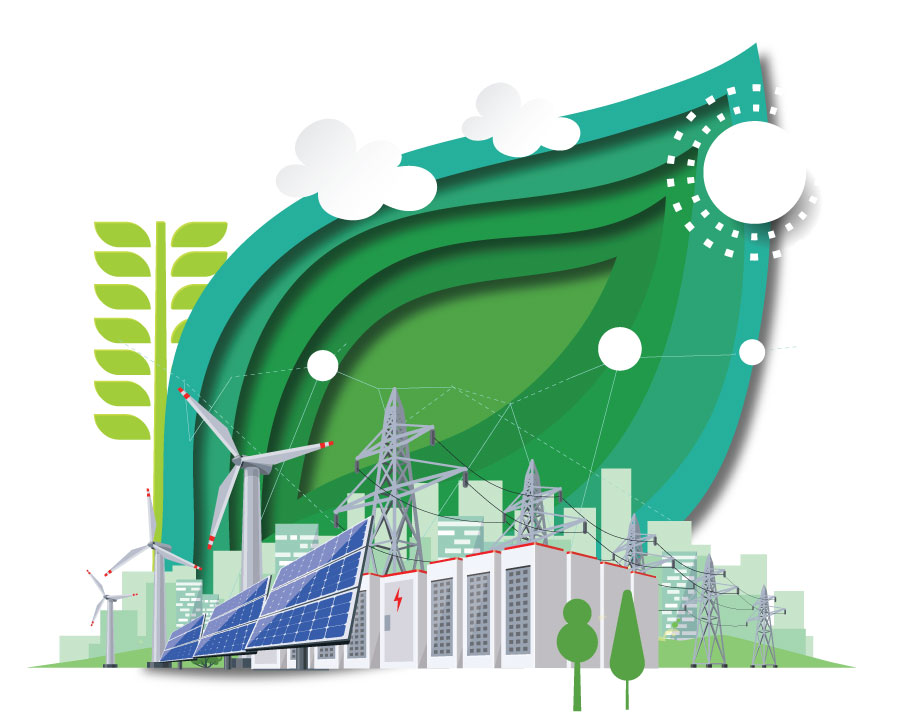
Recent announcements include better batteries, prototype vehicles, as well as new mining and recycling efforts.
It’s been a busy few weeks in the electric vehicle (EV) world. From battery innovations to streamlined technologies and even recycling advances, companies, researchers, and startups are continuing to make strides toward more expanded electrification.
Just this past week, the U.S. Department of Energy (DOE) announced $44.8 million in funding from the Bipartisan Infrastructure Law (BIL) for eight projects that will lower costs of recycling electric drive vehicle batteries and electric drive vehicle battery components, with the long-term aim of lowering vehicle costs. This follows an already allotted $92 million in projects to advance EV battery recycling and expand equitable deployment, all in support of the goal to have EVs comprise half of all vehicles sold in the U.S. by 2030.
Recipients of this latest round of funding include Chillicothe, Ill.-based Caterpillar Inc., which will receive $5 million to develop a new or improved battery pack for off-highway (non-light duty) vehicle batteries that are easier to dismantle. General Motors LLC of Pontiac, Mich., is getting $8 million to develop and demonstrate an automatic sorting and de-hazarding system for end-of-life EV batteries, while ReJoule Inc. of Signal Hill, Calif., will utilize $6 million to develop and scale EV battery diagnostics technology.
Elsewhere, the pursuit of a better battery continues as well. On Oct. 29, Argonne National Laboratory announced a breakthrough of its own, in the form of a “dual-gradient” design for a lithium-ion battery’s cathode, which increases a battery’s energy storage capacity, stability, and lifetime, and cuts costs, which could greatly accelerate EV and grid battery adoption.
More for You: EV Trucks Fight for Traction
High-voltage operation generally causes cathode particles with layered, ordered structures to crack and react more with the battery’s electrolyte, rapidly degrading the cathodes and reducing the battery’s capacity and lifetime. Argonne researchers decided to fabricate cathode particles such that the structure gradually transitions from disordered material on the surface to an ordered, layered material in the core, thus combining the best aspects of different compositions and structures into a single particle.
During testing, these dual-gradient particles were far more durable, losing only about 2 percent of their storage capacity after 500 charge and discharge cycles.
Meanwhile, a Dallas-based startup has developed a strategy that allows a range of lithium batteries to charge within just five minutes without negatively impacting the battery. The technology uses a graphene-based heat spreader to quickly move heat from a battery to warm it up before or during fast charging, paired with a cooling system that activates when the battery is in use in a device or EV. Solidion’s plans are to commercialize this tech over the next several years.
It's Time to Renew Your ASME Membership
Major automakers are in the mix as well. Stellantis has announced its plans to introduce solid-state batteries into a demonstration fleet of Dodge Charger Daytona EVs that will launch by 2026. Woburn, Mass.-based Factorial Inc. is behind this battery technology—Stellantis infused the battery maker with $75 million back in 2021—which has an energy density of more than 390 Wh/kg. These solid-state batteries offer a few advantages over traditional lithium-ion batteries, according to the companies, which include higher energy density and reduced weight, along with improved performance and the potential to reduce lifetime vehicle costs.
But it’s not just the batteries that are critical, but the materials necessary to manufacture them. On Oct. 24, the Bureau of Land Management approved the Rhyolite Ridge Lithium-Boron mining project in Esmeralda County, Nev., which could potentially supply enough lithium to power 370,000 EVs each year. Situated in southern Nevada’s Silver Peak Range, the project will also feature significant protections for the local ecosystem, as lithium mining is well known for having detrimental environmental impacts.
But Stellantis is looking to improve its EVs in other ways—aerodynamically, for one. The automaker recently invested $29.5 million at its research and technical center in Auburn Hills, Mich., to upgrade a wind tunnel with Moving Ground Plane (MGP) technology, which will allow the facility to measure and reduce airflow resistance from wheels and tires. While test vehicles remain static, belts suspended by cushions of air enable wheel movement at all four corners, while a fifth belt runs longitudinally beneath the vehicle, mimicking on-road travel conditions.
Similar Reading: ORNL, Volkswagen Succeed in First 270-kW Wireless Power Transfer to EV
New automation capability will enable researchers to make changes to the wheelbase and track in minutes, versus up to two hours in conventional wind tunnels. Ultimately, the resulting optimized aerodynamic efficiency will help extend EV driving range on a single charge.
Across the pond, French automaker the Renault Group revealed a new demonstration car, the Emblème, at Mondial de l'Auto 2024 in mid-October that emits 90 percent less greenhouse gases over its entire life cycle than a similar vehicle produced today. Its rear-mounted dual-energy electric powertrain is fueled by both electricity and hydrogen. The vehicle’s components have a 70 percent reduction in carbon footprint and 50 percent of the car is made of recycled materials. Nearly all of the materials used on the car can be recycled at the end of life as well.
And speaking of end life, Mercedes-Benz also made news in late October with the opening of Europe’s first battery recycling plant in Kuppenheim, Germany. The facility features an integrated mechanical-hydrometallurgical process that has an expected recovery rate of raw materials such as lithium, nickel, and cobalt of more than 96 percent. These materials will then find use in new batteries for future EVs. This plant also makes Mercedes-Benz the first car manufacturer to close the battery recycling loop with its own in-house facility, the company claims.
Here in the U.S., EVs accounted for 17.9 percent of new light-duty vehicle sales in Q1 2024 and 18.7 percent in Q2, according to Wards Intelligence, continuing the mostly upward trend since the pandemic. As such figures continue to grow, solutions and innovations like these will become even more critical to meet both consumer demand and EV adoption goals.
Louise Poirier is senior editor.
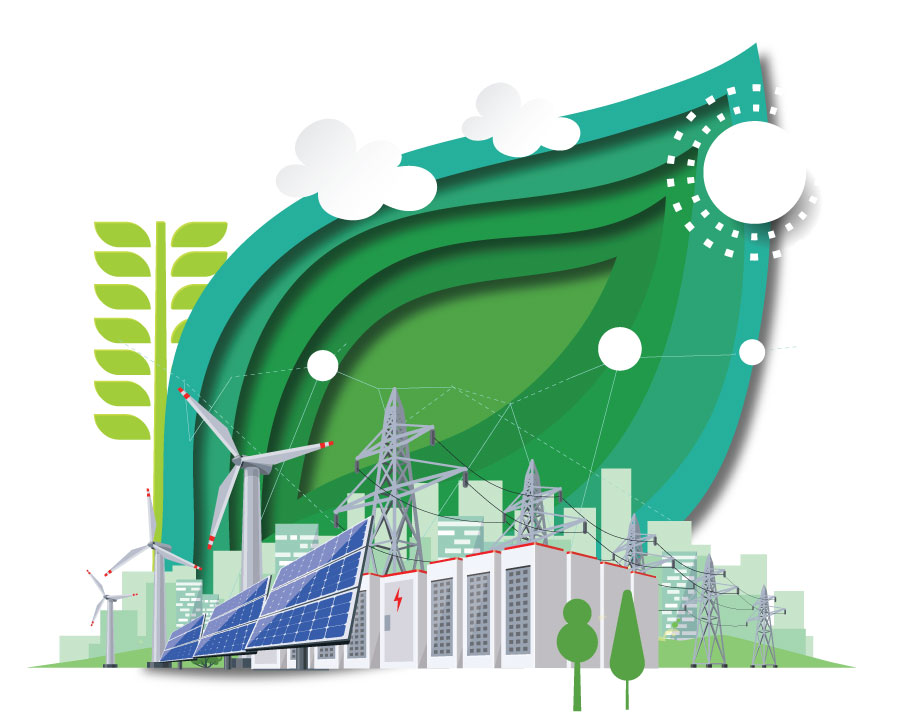
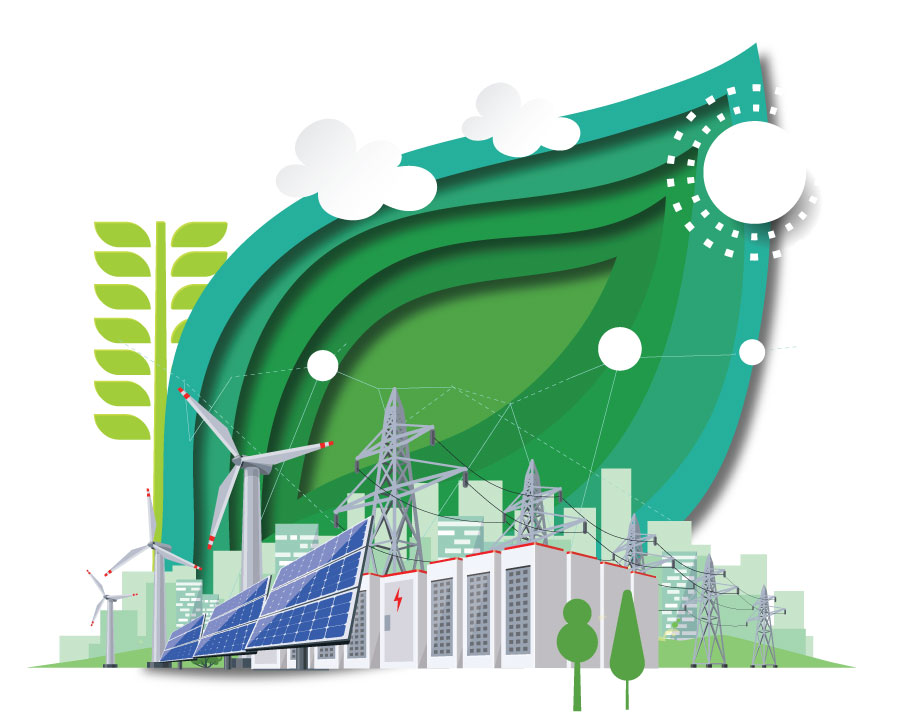