Reducing Cost of Replacement Parts with 3-D Printing
Reducing Cost of Replacement Parts with 3-D Printing
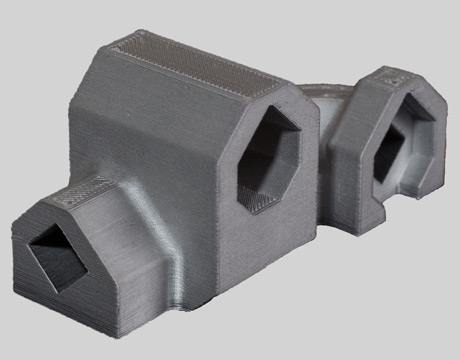
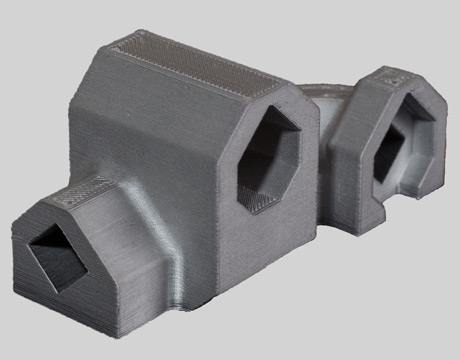
Case Study provided by Markforged
Stanley Black & Decker, an S&P 500 company, is a diversified global provider of hand tools, power tools and related accessories, electronic security solutions, healthcare solutions, engineered fastening systems, and more. By integrating Markforged additive manufacturing technology into their workflow, they eliminated the need for complex warehousing and slashed costs by 12x and lead times by 20x on low-volume replacement parts.
Before utilizing the Metal X, Stanley Infrastructure Innovation engineers faced a lose-lose situation with low-volume replacement parts: either machine parts on demand or keep them in stock.
Unrealistic Ideal
Because the machining infrastructure to create one part is equal to that of batch manufacturing, fabricating one-off parts is prohibitively expensive and requires unacceptable lead times. While it avoids the need to keep inventory, its cost makes it an unworkable solution.
Inefficient Reality
By storing replacement parts in inventory, Stanley Infrastructure always has a part available and leverages lower batch manufacturing costs. However, to support this infrastructure for thousands of parts the company has to keep a massive physical inventory that’s costly to maintain.
Wheel Shaft
The PG10 Profile Grinder used to be machined out of a single block of steel. Because of the size of the flange and the length of the shaft, this wasted ~90% of the stock material in each part. Stanley engineers redesigned the wheel shaft to be a three-part assembly. By purchasing an off-the-shelf shaft and key, they were able to easily print the flange on the Metal X. The printed wheel shaft cam costs $16.38 to print and holds the 90lb frog grinder.
Actuator Housing
The original actuator housing for the PD45 Hydraulic Post Driver consisted of four parts—a cast and machined main housing, laser-cut cover plate, and two bolts to fasten the housing assembly together. Stanley Infrastructure Innovation engineers redesigned the part to print on the Metal X. Instead of a four-part assembly, the redesigned part prints in one piece without supports. The actuator housing costs less than $20 to print and took less than two days from design to final part.
Stanley Infrastructure Innovation tested three identical parts printed on the Metal X. These parts proved durable through tens of thousands of cycles and strong enough to handle significant compressive load. Replacing their current manufacturing workflow with the Metal X allowed Stanley Black & Decker to save between 34% and 48% on manufacturing costs and slashed 69% of part lead time. While these are significant savings, Stanley Black & Decker leveraged the use of its Metal X even further by supplanting their process of single replacement parts for devices in the field.
Printing single parts with the Metal X proved 12.5x cheaper and 20x faster than the company’s existing process of casting and machining in batches. The Metal X further undercut this process by being a pay-per-part machine instead of a pay-per-batch machine. According to a Stanley Infrastructure Innovation engineer, “It is very feasible to leverage the Metal X platform in additively manufacturing the discussed actuator housing with very minimal capital and time investment.” They believe that they can save thousands of dollars per year on this part alone, while replicating the part quality and reliability that they expect from machined parts.
Learn more about metal and composite additive manufacturing solutions at markforged.com.
Recommended for You: Mechanical Engineering magazine’s Manufacturing Special Report
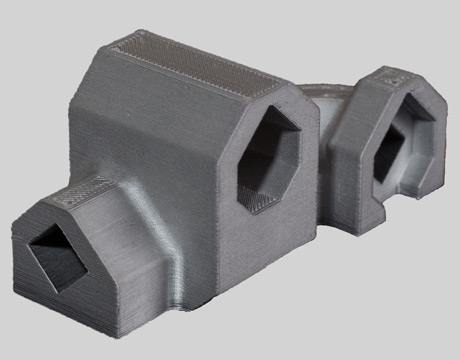
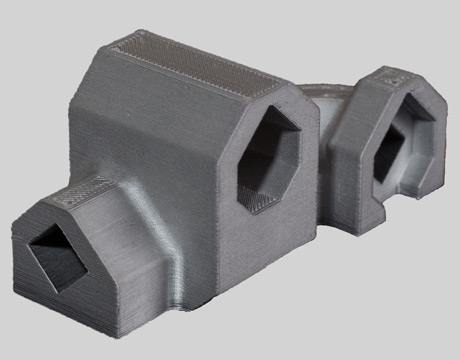