Helmets That Absorb and Respond to Collisions
Helmets That Absorb and Respond to Collisions
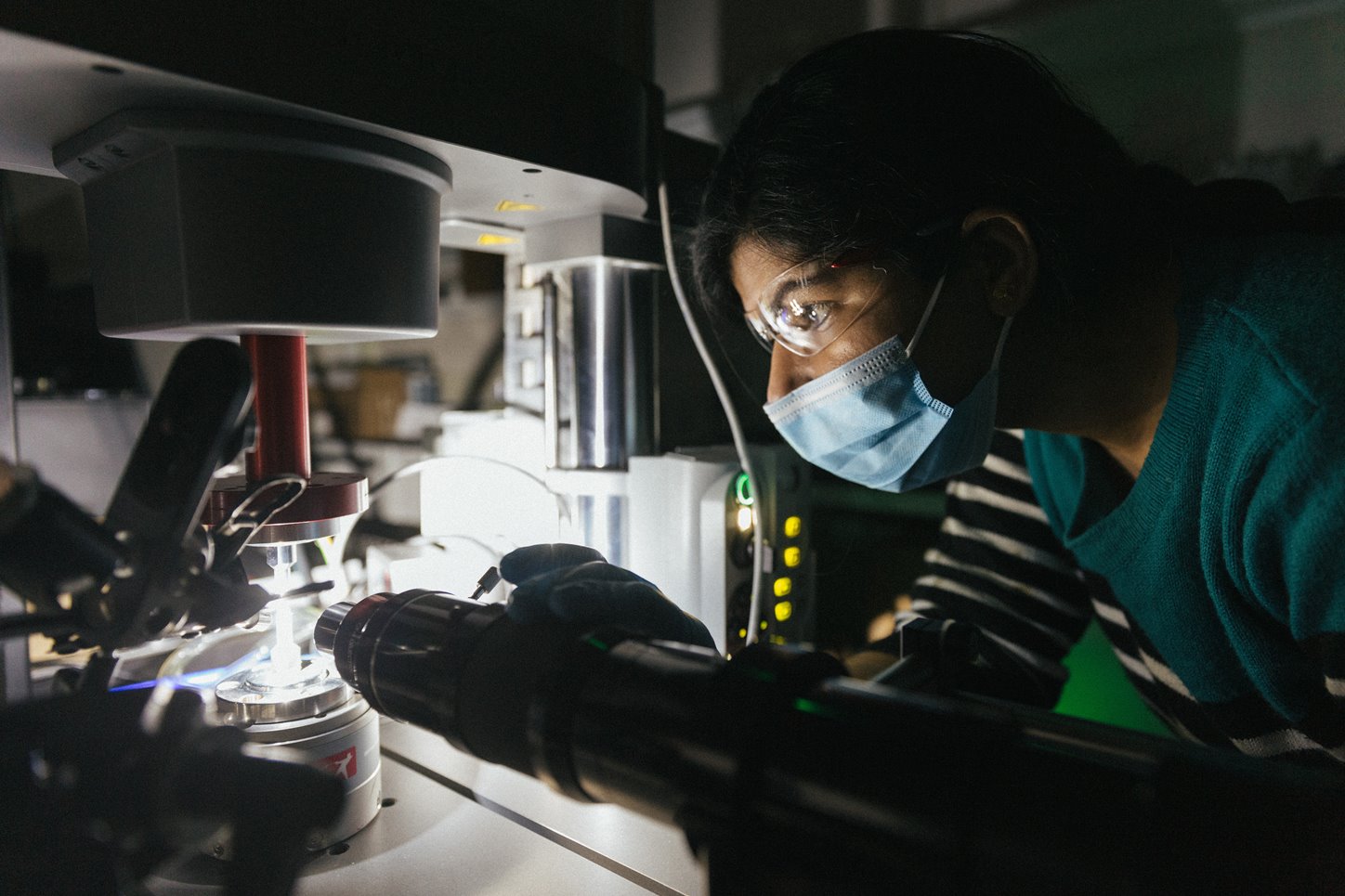
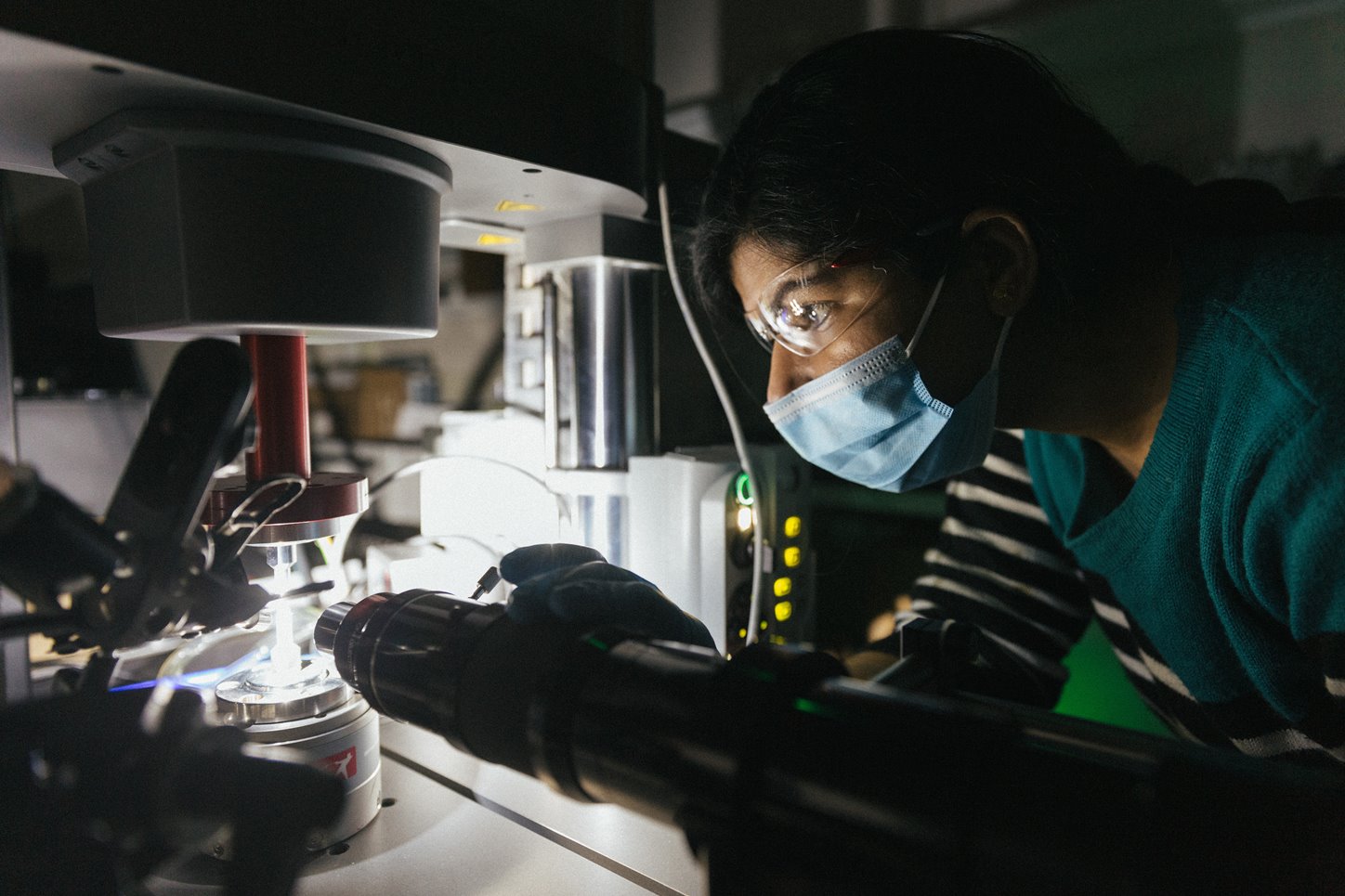
Engineers are working with helmet makers to protect the brain against concussions and subdural hematomas using technology that makes them more durable, lighter, stronger, and responsive.
In the past, people wore helmets to protect against a blow to the head that could cut or fracture the skull. Yet, doctors have found that the skull and brain within it suffer debilitating damages from hidden, and often less-obvious trauma such as concussions or subdural hematomas. So engineers are working with helmet makers to protect the brain using technology that reaches beyond a tough outer shell and soft padding.
Currently a helmet's impact-absorbing layers work to spread a collision over a larger area over longer time. Materials that are better at absorbing and dissipating a collision's kinetic energy can mitigate, or even prevent injury, by slowing or stopping it before it reaches the brain. That is where an initiative led by University of Wisconsin-Madison scientist Ramathasan Thevamaran comes in.
Become a Member: How to Join ASME
The assistant professor of mechanical engineering has created a material that has 18 times higher specific energy absorption than the foam currently used in U.S. military combat helmet liners. “This new material holds tremendous potential for energy absorption and thus impact mitigation, which in turn should significantly lower the likelihood of brain injury,” he explained.
Thevamaran turned to carbon nanotubes because it's a proven technology known for its strength, light weight, and ability to perform in extreme environments—both very high heat or extremely low temperatures. "Because it's a fiber, through synthesis, there's a lot you can control—its density and stiffness, for example," he explained.
To create the new material—an architected vertically aligned carbon nanotube foam—Thevamaran and his team enhanced its mechanical properties by designing a architecture consisting of numerous micrometer-scale cylinder structures, each made of many carbon nanotubes. His process is explained in detail in a paper recently published online in the journal Extreme Mechanics Letters.
Similar Reading: New Nanomaterial Proves Stronger Than Kevlar
Finding the new foam’s ultimate optimal design parameters, such as the thickness of the cylinders, their inner diameter and the gap between adjacent cylinders, took the researchers looking at 60 different combinations and conducting three tests on each sample, or 180 experiments. They systematically varied each parameter and studied all possible combinations. They finally found that cylinders with a thickness of 10 micrometers or less, arranged close to each other, produced a foam with the best shock-absorbing properties.
Between head and helmet
But a strong outer shell and durable, shock-absorbing foam doesn't always address how the head rotates during an accident. Half a world away, Madelen Fahlstedt, a biomechanical specialist working for the Swedish company Mips AB (PUBL), focuses on the rotational motion that occurs during oblique impacts. Mips is an ingredient brand working with helmet manufacturers.
"When you fall from a bike or on a ski slope, you will probably not fall straight. It will probably be at an angle, an oblique impact," she explained. At the moment of impact, tangential force can make the head rotate and change direction. Because the brain consists primarily of water, it is sensitive to shear deformations. Shear refers to unaligned forces pushing the brain in two different directions.
Research has shown that more than likely the cause of concussions are impacts on the head including rotational motion. Also, subdural hematoma (bleeding between the brain and the skull bone) can be caused by rotational movements of the head, resulting in overstretching of the bridging veins supporting the brain with blood. This means the brain is very sensitive to rotational forces.
"You want to try to redirect or disperse the motion away from your head, possibly with a system designed to help mitigate rotation intended to better direct the rotational energy," Fahlstedt explained.
The Mips system is made of strong poly-carbonate coated with a proprietary layer that allow less friction. It works inside the helmet and allows a multi-directional movement of 10 to 15 mm on certain angled impacts. It is designed to re-direct rotational energy with the intention to help mitigate the effect of rotation acting on the head during an angled impact. The sliding movement occurs during the first 5 to 10 milliseconds of the impact event.
Next steps
Thevamaran and his team of researchers are patenting their innovation through the Wisconsin Alumni Research Foundation, and the university-industry collaboration was part of the UW-Madison led PANTHER program, an interdisciplinary research initiative that is developing solutions to enable better detection and prevention of traumatic brain injuries. The researchers’ are currently working with helmet manufacturer Team Wendy. The manufacturer is experimenting with a helmet liner prototype made from the new material to measure its performance in real-world scenarios.
Fahlstedt's team continues with Mips research and testing, hoping to make licensing Mips’ technology an attractive solution for helmet makers. For example, industrial construction helmets were not considered an obvious application to benefit from systems intended to help mitigate rotational motion, but Mips’ research found otherwise.
Cathy Cecere is Membership Content Program Manager.
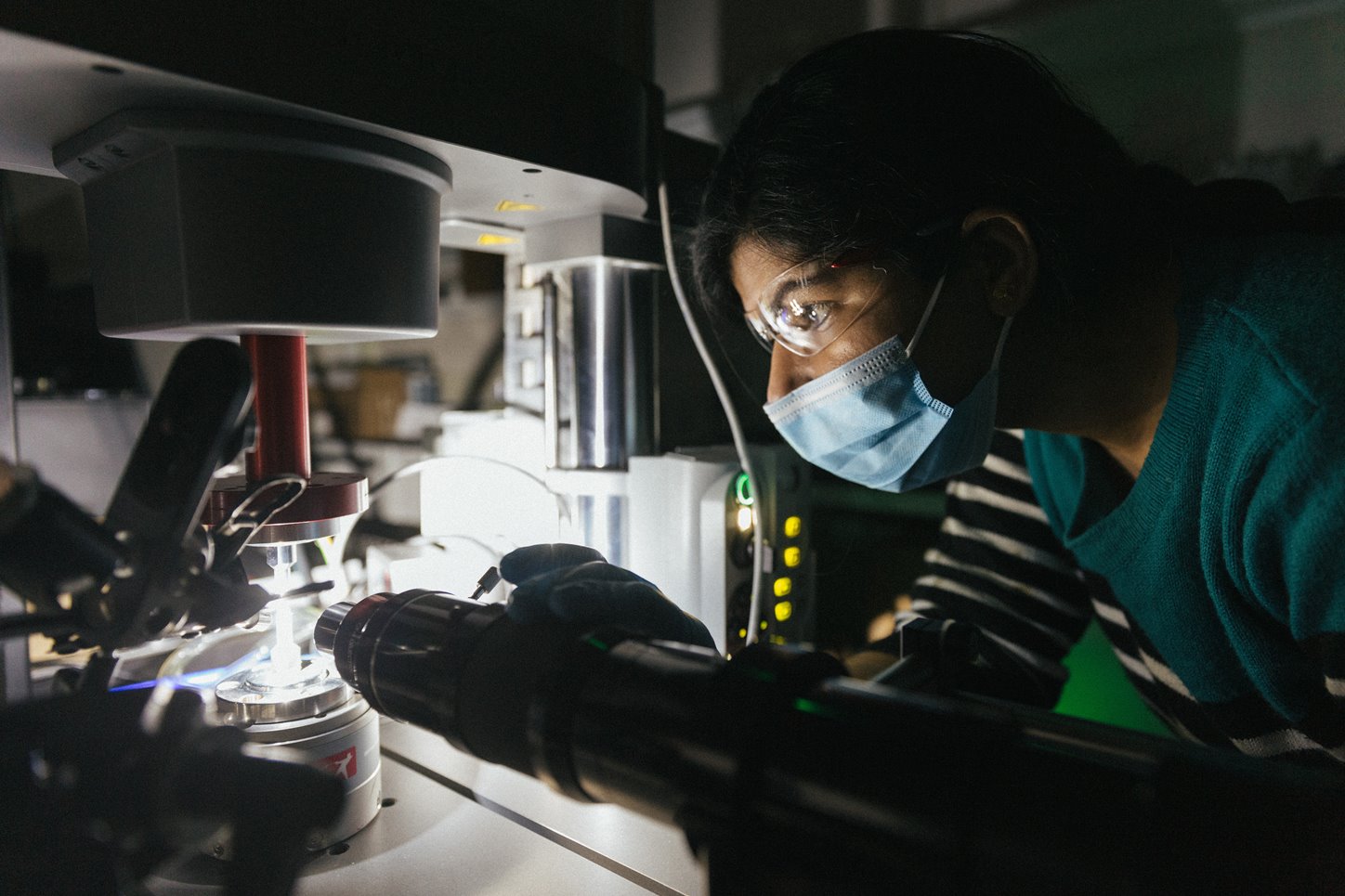
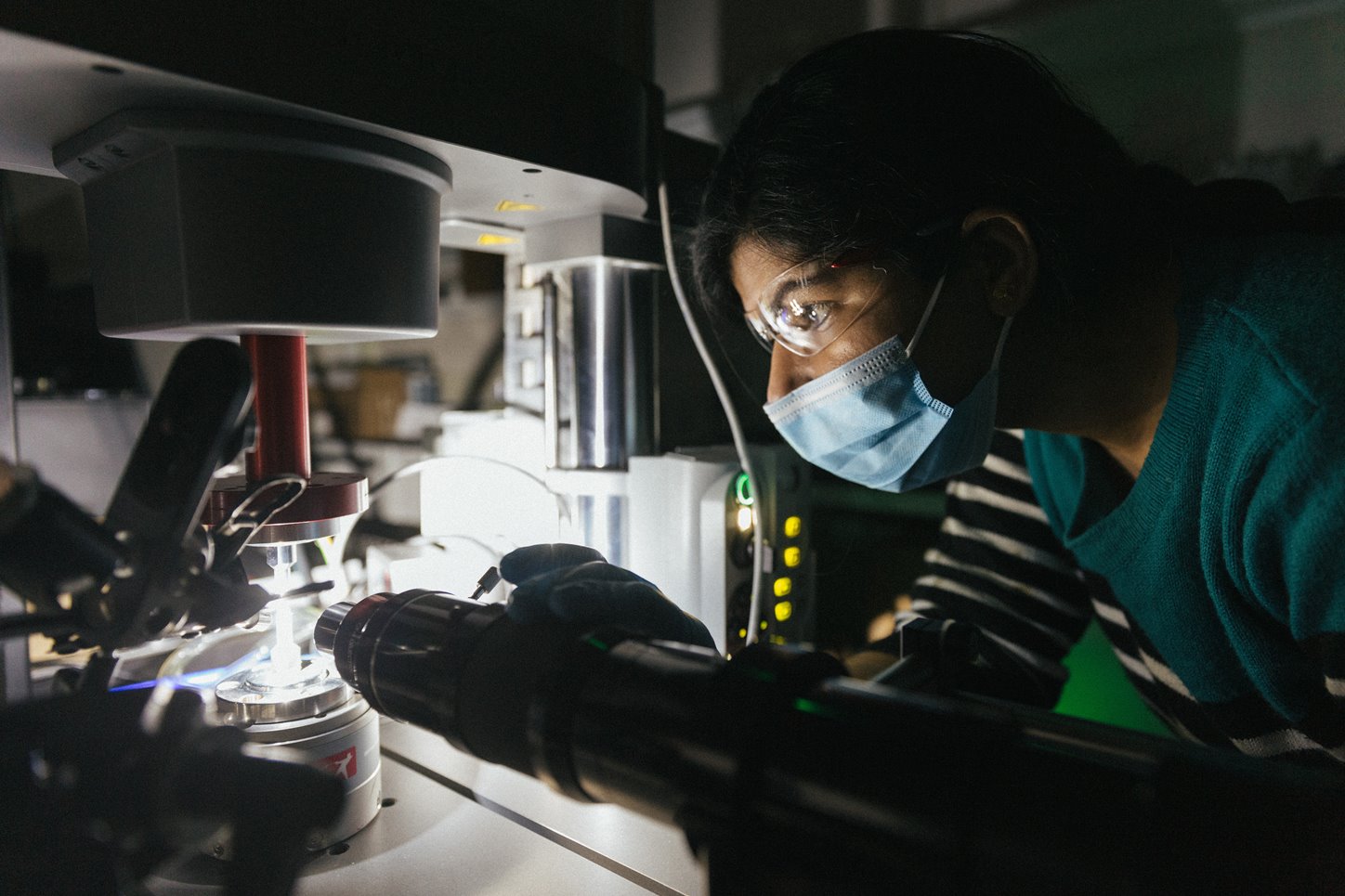