Espinosa is a professor in the Department of Mechanical Engineering at Northwestern University. Jin was a postdoctoral researcher in the Division of Engineering and Applied Science at the California Institute of Technology when the paper was published; currently, Jin is a senior research scientist at Washington University in St. Louis.
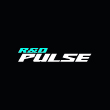
We hear about metamaterials a lot these days for all the incredible applications they continue to unlock. What drew you toward studying mechanical metamaterials and what makes them so attractive for engineering compared to other types of metamaterials?
Espinosa: Our interest in mechanical metamaterials was sparked by the unique opportunity they present to engineer materials de novo, where architecture plays a crucial role in addition to material composition. Unlike traditional materials, whose properties are primarily determined by their chemical makeup, mechanical metamaterials derive their remarkable mechanical properties—such as strength, stiffness, and resilience—directly from their structural design at various length scales. This opens a vast array of possibilities for creating materials with properties that are finely tuned for specific applications.
What makes mechanical metamaterials particularly attractive for engineering is their versatility and scalability. For instance, by adjusting the architecture, we can create materials that are extremely lightweight yet incredibly strong, or materials that can absorb impact energy much more efficiently than conventional materials. This tunability is invaluable for applications in aerospace, automotive engineering, devices, and even biomedical devices, where performance often hinges on achieving the perfect balance of strength, weight, and functionality.
In comparison to other types of metamaterials, mechanical metamaterials stand out because they are directly applicable to load-bearing applications, which are fundamental to most engineering disciplines. While other metamaterials, such as photonic or acoustic metamaterials, are typically designed to manipulate waves—whether light, sound, or electromagnetic—mechanical metamaterials address the very tangible and critical demands of structural integrity and mechanical performance.
In essence, the field of mechanical metamaterials is not just about discovering new materials but about pioneering a new way of thinking about material design. This shift from material composition to structural architecture is what drew us to this field, and it continues to drive our research in the quest to uncover new possibilities and applications.

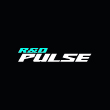
What have been the top two or three most significant recent advances in self-assembly techniques when it comes to mechanical metamaterials? And why is self-assembly so significant?
Jin: Recent advances in self-assembly techniques have significantly propelled the field of mechanical metamaterials, with a few key developments standing out.
One of the most significant recent advances is the use of colloidal nanocrystals to create highly ordered and architected superlattices. These nanocrystals can be precisely functionalized and assembled into various lattice structures that exhibit exceptional mechanical properties. The ability to tailor these properties by modifying the nanocrystals’ surface chemistry and assembly conditions has opened new possibilities for creating materials with tunable stiffness, strength, and resilience at the nanoscale. The scalability of this technique is particularly promising for engineering applications where both precision and large-scale production are required.
Another groundbreaking advance is the incorporation of DNA techniques in the fabrication of mechanical metamaterials. By leveraging the precision of DNA self-assembly, researchers have been able to construct complex nano-architectures with exceptional mechanical properties. For example, DNA-stabilized structures have demonstrated superior compressive strength, making them ideal candidates for lightweight, high-strength materials in aerospace and other high-performance applications.
The integration of machine learning (ML) and automation in the self-assembly process is another breakthrough. By automating the assembly process and using ML algorithms to optimize design parameters, researchers can now rapidly explore vast design spaces and produce materials with highly optimized properties. This approach not only speeds up the discovery process but also improves the reproducibility and scalability of self-assembled mechanical metamaterials.
Self-assembly is significant because it offers a scalable, bottom-up approach to fabricating materials with precise and complex architectures that would be challenging or impossible to achieve with traditional top-down manufacturing methods. The ability to control material properties at the nanoscale through self-assembly enables the creation of metamaterials with unparalleled mechanical characteristics, such as high strength-to-weight ratios and resilience to impact, which are critical for advanced engineering applications.

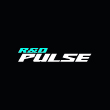
In the paper, you mentioned foreseeing “mechanical metamaterials fabricated from self-assembly techniques impacting a variety of applications.” What kinds of applications will benefit the most from these materials? Are there some potential applications that haven’t yet been explored that you believe hold promise as well?
Espinosa: They have the potential to revolutionize a wide range of applications, particularly in fields where lightweight, strong, and resilient materials are critical.
In aerospace and defense fields, the demand for materials that offer high strength-to-weight ratios is paramount. Mechanical metamaterials created through self-assembly can provide unprecedented performance, such as superior impact resistance and energy absorption capabilities. This makes them ideal for use in aircraft, spacecraft, and protective equipment where minimizing weight without compromising strength is crucial.
The biomedical field can greatly benefit from these materials as well, especially in the design of implants and other medical devices that require biocompatibility, mechanical robustness, and precision at small scales. For example, self-assembled metamaterials could lead to the development of implants that better mimic the mechanical properties of natural tissues, leading to improved patient outcomes.
Mechanical metamaterials with tailored mechanical, thermal, and optical properties can be used to create advanced microelectronic components and photonic devices. These materials can help in thermal management and reducing device sizes while improving performance, which is essential for the ongoing miniaturization trend in electronics.
As for potential applications that haven’t yet been fully explored, one promising area is soft robotics. Self-assembled mechanical metamaterials could be used to design soft robotic components that are both lightweight and capable of withstanding significant deformation without losing functionality. These materials could enable the creation of robots that are more flexible, resilient, and capable of operating in complex, unstructured environments. Another unexplored area is programmable materials, where the dynamic response of mechanical metamaterials could be harnessed for applications requiring materials that change their properties in response to external stimuli, such as temperature, light, or pressure. This could lead to innovations in adaptive structures, smart textiles, and even shape-memory and self-healing materials.

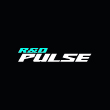
Is there an ideal fabrication method for mechanical metamaterials at the moment? What are the topmost challenges that current methods must overcome?
Jin: Currently, there isn't a single ideal fabrication method for mechanical metamaterials, as the choice of method depends heavily on the specific application, desired properties, and scale of production. However, several techniques have shown great promise, each with its own strengths and limitations.
Additive manufacturing techniques, such as two-photon polymerization (TPP) and direct ink writing (DIW), are highly versatile and allow for the creation of complex 3D architectures with precise control over geometry. These methods are ideal for rapid prototyping and producing custom designs with microscale features. However, they often struggle with scaling up to larger sizes and achieving nanoscale resolution remains challenging.
Self-assembly, particularly colloidal nanocrystal and copolymer self-assembly, offers a bottom-up approach to fabricating materials with nanoscale precision over large areas. This method is particularly well-suited for applications requiring uniform properties at the nanoscale. However, challenges in controlling defects, achieving reproducibility, and scaling up from laboratory to industrial scales still exist.
Combining top-down methods, like photolithography or AM, with bottom-up self-assembly offers a promising route to overcome the limitations of each individual technique. These hybrid approaches can provide the precision and scalability needed for engineering applications. However, they are often complex and require careful alignment between the different scales of fabrication.
One of the biggest challenges is scaling up the fabrication of mechanical metamaterials from the laboratory to practical, industrial scales. While self-assembly offers scalability in terms of surface area, achieving consistent quality and defect control over large volumes remains difficult. Additionally, additive manufacturing methods can be slow and expensive when applied to large-scale production.
High-resolution techniques like TPP offer excellent precision but at the cost of speed, making them less practical for large-scale applications. Conversely, faster methods like DIW may compromise on the fine details, limiting their use in applications requiring nanoscale features.
Managing defects during the fabrication process is crucial, especially for self-assembled materials where imperfections can significantly impact mechanical properties. Ensuring reproducibility across different batches is another challenge, particularly when dealing with complex architectures.

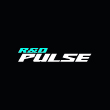
What are you and your teams looking to uncover next as your research into these materials continues?
Espinosa: We’re exploring several key areas that may unlock new possibilities and further advance the field.
One of the most intriguing directions is the application of mechanical metamaterials to study and influence cell behavior, particularly in the context of cell-extracellular matrix (ECM) interactions. The ECM provides structural and biochemical support to surrounding cells, and its mechanical properties are crucial for cellular functions such as differentiation, migration, and proliferation. We’re studying how precisely engineered mechanical metamaterials can mimic the mechanical properties of the ECM at various scales. By creating environments that closely replicate the physical cues cells experience in vivo, we anticipate gaining deeper insights into how cells respond to mechanical stimuli, which could lead to new strategies in tissue engineering and regenerative medicine. Building on the understanding of how architected ECM controls cell environments, we plan to explore their integration in microfluidic devices for cell manipulation and analyses—for example, using localized surface plasmon sensing and confocal microscopy.
We’re also exploring the development of dynamic metamaterials that can change their properties in response to environmental cues, much like how the ECM can remodel itself in response to cellular activity. These adaptive materials could be used to create scaffolds that evolve along with the tissue they support, providing a more responsive and supportive environment for tissue regeneration. For example, we’re interested in materials that can stiffen or soften in response to mechanical forces exerted by cells, thereby guiding tissue development in a controlled manner.
We’re also advancing the integration of ML into the design process of mechanical metamaterials. There is a need to develop more sophisticated ML-assisted inverse design frameworks that can efficiently explore vast design spaces and predict the optimal material architectures for desired mechanical properties. This approach will not only accelerate the discovery of new metamaterials but also provide deeper insights into the underlying principles that govern their behavior.

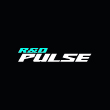
Would you like to share any final thoughts with our readers?
Jin: We would like to emphasize that we are at a truly exciting juncture in the field of mechanical metamaterials. The convergence of advanced fabrication techniques, such as self-assembly, with powerful computational tools like ML, is transforming how we think about material design. What was once the realm of theoretical possibility is now becoming a practical reality, enabling us to create materials with properties that can be precisely tuned for a wide range of applications.
As we continue to explore these new frontiers, collaboration across disciplines will be key. Mechanical metamaterials sit at the intersection of materials science, engineering, chemistry, physics, and computer science. By fostering interdisciplinary collaboration, we can accelerate the pace of discovery and innovation, bringing us closer to realizing the full potential of these extraordinary materials.
We also want to encourage the next generation of engineers and researchers to dive into this field. There are still many challenges to overcome and questions to answer, but the opportunities for impact are vast. Whether it’s developing new materials for sustainable energy, advancing healthcare technologies, or exploring the limits of what’s possible in aerospace, mechanical metamaterials offer a wealth of opportunities to make a significant difference.
