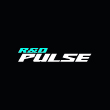
New circular economy policies in the European Union will affect mechatronic products more than any others. How soon do manufacturers need to be ready for that?
The European Commission wants to be fully circular by 2050—and our work is focused on Europe—so that was part of what drove us to pursue the research. Even sooner than that, by 2025, the energy label that we have here in Europe for consumer electronics will include not just the energy consumption and information related to efficiency, but also a new repairability index score. Smartphones, tablets, and soon laptops will be graded with letters—A, B, C, D, etc. And with that you will be able to know how repairable that product is. It will also be mandatory for those smartphones and tablets to have spare parts available for at least seven years. Engineering design plays a key part as the regulations for those products are changing, and manufacturers are obliged to follow that.

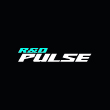
What motivated you to focus on repairability of mechatronic products in your research?
Repairability is one of the easy aspects that we can work on to reduce waste production. And it's one of the inner loops for the butterfly diagram for circularity. For those who don’t know, the circularity assessment of a product’s lifecycle is to first reuse and maintain it, and if it cannot be maintained, to repair it. If it’s beyond reparation, then refurbish or remanufacture it if possible. Our last option in circularity is recycling the product. So, we wanted to give designers the tools to be able to really design with repairability in mind during the early stages of their product development. Reuse of mechatronic products was also an option for the research here, but repairability was more relevant to my background.

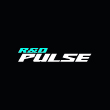
Let’s discuss the four-phase methodology in your paper. How does it work?
Our methodology was based on the reports available from the European Commission. The first step is identifying the target components. Right now, that’s done based on failure analysis. You look at the parts that present a higher failure rate and have the biggest impact if they fail. The example used in our paper is the motor in an oven: If the motor fails, the entire oven fails. What’s lacking right now from regulations is a standard definition of those critical parts—we currently only have a list for smartphones and tablets, but the goal is to have it for all categories. Another approach is to analyze the spare parts market: If everyone is buying a certain component, that implies its failure rate might be higher. Secondly, we disassemble the product for experimentation. This can be done manually or virtually—you don’t really need the physical product if you are able to understand how it is connected because we’re retrieving information about the joining method. For example, whether we’re using reusable fasteners or adhesive or welding components, the types of tools we need, the disassembly depth, and the time we put into removal are all important parameters for calculating an accurate result. Again, here we need to base the information retrieval on the European standard. Third is the assessment, which can be done almost automatically once we have the data spreadsheet of the parameters. We compare the results with a threshold and pinpoint the underlying issues in disassembly. And finally, we develop eco-design actions for the product we’re analyzing. We proposed to define that based on a cost benefit analysis, using the ROC curve method to see if the benefit was higher or not. Thanks to this methodology, we can identify the criticality of components, such as a tool we’re using, or the fastener. And through that we create a repository of eco-design action.

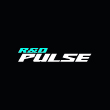
How is your methodology an improvement to the status quo?
There wasn't a methodology to assess repairability for designers. The standard we have provides us with a score, but if you don’t know how to interpret that score or propose eco-design actions based on that result, it’s no help to the designer. If they see a score lower than 0.5, they know there’s a problem, but not why. Our methodology connects the problem with the solutions and proposes guidelines for designers. If we identify a lengthy duration for disassembly for unfastening or an uncommon tool needed for unscrewing something, we can easily propose a solution like changing the fastening method. Right now, our proposal is the only one available in the current literature.

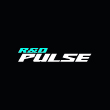
You mentioned using the virtual method in your experimental disassembly. Can you tell us more about how that went?
We actually performed manual disassembly for the first retrieval of information because we have the product. But when we found the criticalities in this case, and we applied the eco-design actions, we used the CAD model instead. With the CAD software, you can see the joining methods, so you are able to virtually remove the parts. The only downside is you are not able to properly address the disassembly time because you're not actually performing it. But we solved this by using a methodology which is based on the MOST technique (Maynard Operation Sequence Technique)—you establish the sequence, and with that sequence, you obtain a standardized time. That makes the virtual results comparable to the manual.

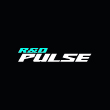
In your case study, you tested the methodology on an electromechanical oven. What made you select that product?
My Ph.D. was focused on cooking appliances, so we have a lot of them available. We found studies already done on cooker hoods, hobs, etc., but not for ovens. The oven model we chose is one of the more complex—it combines with steam, so it has more components than a basic oven would have. From a designer's point of view, it’s an interesting product because there’s a lot to play with. The challenge of disassembling something for the first time when you’re not an expert is you don't really have guidelines to follow. For laptops or other consumer electronics, there are plenty of resources available online, but not with ovens yet. We contacted manufacturers and even attended workshops to understand all the components and the joining methods they use. When you’re doing a repairability assessment, you have to address the easiest way to remove the component. That requires you to understand the product perfectly.

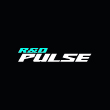
Were there other collaborators besides the product manufacturers that made this an interdisciplinary study?
There were various departments we consulted on the manufacturing side, like life cycle assessment and the R&D department. From our side, we had different backgrounds in engineering expertise. I'm more of a mechanical engineer, and we worked alongside material engineers and industrial engineers as well.

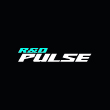
What challenges did you see during your research that future works will need to look out for?
The politics and the timing are the challenges to meet. We know that in three years, we’ll be seeing repair scores on the product labels in Europe. We need to integrate the standards for priority parts and be able to apply the methodology to a full range of products. And we know that the digital product passport is coming to Europe in 2027 and will be implemented for batteries and textiles, and iron and steel are also expected to have a digital passport. It’s critical to get a head start now defining the repairability information that we’ll need to put in those product passports and labels for end consumers and professional repairs.

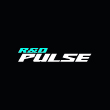
Sarah Alburakeh is strategic content editor.