The Saugus Ironworks Launched American’s Iron Industry
The Saugus Ironworks Launched American’s Iron Industry
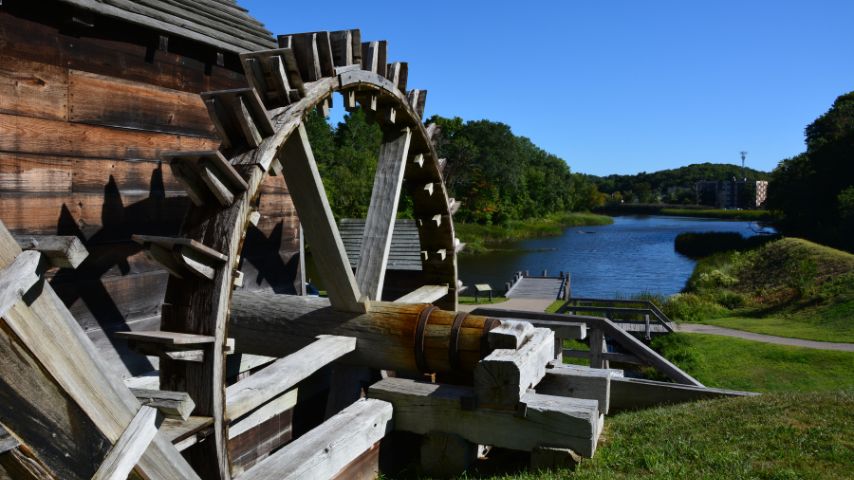
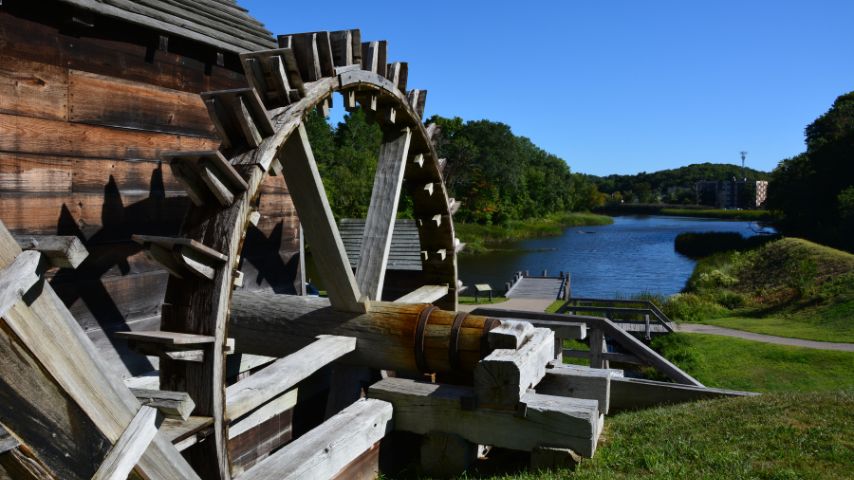
Only 25 years after the Pilgrims landed in North America, engineers started a viable ironworks. Using the same processes used today, the Saugus Ironworks were an impressive technological achievement.
Tucked in the small town of Saugus, Mass., among busier Greater Boston municipalities, may be the best-kept secret of the National Park Service. Indeed, in 2023 only 41,000 visitors stopped by this 12-acre National Historic Site and ASME Landmark.
The Saugus Ironworks, which became a landmark in 1975, is where America’s iron and steel industry was born. Today, the site on the bank of the Saugus River contains a museum, reconstructed industrial buildings, working waterwheels, blacksmith shop, 7th-century home, herb garden, nature trail, picnic area, visitor center, and dock.
The first commercially viable ironworks in North America, the Saugus Ironworks was an impressive technological achievement that operated on the Saugus River from 1646 to 1670. For the making of iron, the location seemed idyllic. “A navigable river, deep forests, and iron ore,” explained Emily Murphy, curator for Salem Maritime National Historic Site and Saugus Iron Works National Historic Site. “Some might even say having all those resources in one place was a divine providence.”
But intervention from God had less to do with the ironworks success and more to do with investors looking out for their investment, Murphy said. “The ‘Undertakers of the Iron Works’ made sure they hired highly accomplished iron workers,” she pointed out. With a secured charter, construction started in 1646, and the furnace was in blast in 1647. The workers followed the same basic processes that are used today. Only steel, except in very small quantities, was beyond the capabilities of the colonists. Ore came from nearby ponds and bogs, stone flux was mined at nearby Nahant, the forest provided charcoal, and the river supplied waterpower.
In the 1600s, the area was known as Hammersmith. But we “actually don't know a lot about the village,” Murphy explained. According to historian E. N. Hartley, about 185 people were paid for full- or part-time work for the Iron Works. Of those, about 35 were skilled iron workers, but not everyone lived in the village. Many of the part-time workers were from local farm families. “What was most unusual about [the Iron Works] was that it was integrated. You could go from raw ore to finished nail rod in one place,” Murphy said. This was not a common situation. According to historian Hartley, in the book Ironworks on the Saugus, there were only a dozen of these integrated iron works in the Western world at the time.
Visitors to the site today can witness demonstrations during guided tours of the Iron Works, explained Andrew Donovan, supervisory park ranger for interpretation at Salem Maritime National Historic Site and Saugus Iron Works National Historic Site. “We run the waterwheels that help visitors better connect with the work that was happening at Hammersmith,” he said.
The original site had a fieldstone-shelled furnace that was 24 feet square at the base and about as tall at its height. It had a hollow core that workers would shovel alternate layers of materials. “As you can imagine, it was very difficult and dangerous work,” Murphy explained. Leather bellows, operated from a water wheel, supplied the blasts of air at the furnace base.
Molten iron collected in the hearth. Meanwhile, impurities were coalesced by the flux into a slag, which floated on it. Workers would eventually break open the sides of the hearth (that were temporarily sealed with clay) and tapped the slag and iron. It was either cast in molds for utensils, kettles, or stove fronts or, more often, run in open, branched trenches where it solidified into "sows" and “pigs."
The refinery and chafery were housed in another building. In the refinery, workers melted the iron on a bed of glowing charcoal under blasts of air (allowing oxidation remove residual carbon). Workers then took this heavy, hot, and unwieldly mass (it is difficult to completely liquefy pure iron on a forge hearth) and lifted it out and worked and squeezed it under the power hammer into short, rough rectangular bars, called "blooms." They then took the blooms and reheated them in the chafery and shaped them into long wrought iron bars—the iron work’s main product.
Become a Member: How to Join ASME
In yet another building, workers took a portion of the iron bar and further refined it in a rolling mill. Parallel iron rolls driven by a water wheel with wooden pins for teeth reduced the reheated bar to flat strips, and workers took these and slit them into rods to make nails. The labor was difficult and “the workers had little protection beyond heavy leather gloves and aprons,” Murphy said.
A hidden secret of the site is that it hosts visitors picnicking, dog walking, or taking photos, Donovan said. In fact, the Commonwealth of Massachusetts boasts more wooded areas today than it had in the 1600s. And this was an issue for the early ironworkers. “They had to worry less about ore and gabbro running out and more about the trees for charcoal,” Murphy said.
“A ton of iron needed three tons of ore, two tons of gabbro, and 265 bushels of charcoal, and the Saugus blast furnace could produce six to seven tons of iron a week,” she explained. “There was no competition for the ore and gabbro, but the ironworks had to compete with the growing population of the colony and other industries for the wood to produce charcoal.”
Hammersmith wasn’t as long-lived as many of its successors. It wasn’t financially successful and seldom saw a profit. When the local bog ore became exhausted, importing resources was an expensive proposition. Meanwhile, foreign iron was getting cheaper. But despite the resource situation, “mismanagement of the iron works may have been the final situation that doomed the site,” Murphy speculated.
Read ASME's Landmark Description: Saugus Ironworks
Today, visitors enjoy “exploring the grounds and visiting the free museum at the park,” Donovan explained. “Inside the museum, you can see iron-making artifacts from the 1600s.” You can also find indigenous tools and colonial artifacts that illustrate how the Saugus River was used by diverse groups that have lived in the area over the years.
Cathy Cecere is membership content program manager.
The Saugus Ironworks, which became a landmark in 1975, is where America’s iron and steel industry was born. Today, the site on the bank of the Saugus River contains a museum, reconstructed industrial buildings, working waterwheels, blacksmith shop, 7th-century home, herb garden, nature trail, picnic area, visitor center, and dock.
Divine providence
The first commercially viable ironworks in North America, the Saugus Ironworks was an impressive technological achievement that operated on the Saugus River from 1646 to 1670. For the making of iron, the location seemed idyllic. “A navigable river, deep forests, and iron ore,” explained Emily Murphy, curator for Salem Maritime National Historic Site and Saugus Iron Works National Historic Site. “Some might even say having all those resources in one place was a divine providence.”
But intervention from God had less to do with the ironworks success and more to do with investors looking out for their investment, Murphy said. “The ‘Undertakers of the Iron Works’ made sure they hired highly accomplished iron workers,” she pointed out. With a secured charter, construction started in 1646, and the furnace was in blast in 1647. The workers followed the same basic processes that are used today. Only steel, except in very small quantities, was beyond the capabilities of the colonists. Ore came from nearby ponds and bogs, stone flux was mined at nearby Nahant, the forest provided charcoal, and the river supplied waterpower.
In the 1600s, the area was known as Hammersmith. But we “actually don't know a lot about the village,” Murphy explained. According to historian E. N. Hartley, about 185 people were paid for full- or part-time work for the Iron Works. Of those, about 35 were skilled iron workers, but not everyone lived in the village. Many of the part-time workers were from local farm families. “What was most unusual about [the Iron Works] was that it was integrated. You could go from raw ore to finished nail rod in one place,” Murphy said. This was not a common situation. According to historian Hartley, in the book Ironworks on the Saugus, there were only a dozen of these integrated iron works in the Western world at the time.
Advanced technology
Visitors to the site today can witness demonstrations during guided tours of the Iron Works, explained Andrew Donovan, supervisory park ranger for interpretation at Salem Maritime National Historic Site and Saugus Iron Works National Historic Site. “We run the waterwheels that help visitors better connect with the work that was happening at Hammersmith,” he said.
The original site had a fieldstone-shelled furnace that was 24 feet square at the base and about as tall at its height. It had a hollow core that workers would shovel alternate layers of materials. “As you can imagine, it was very difficult and dangerous work,” Murphy explained. Leather bellows, operated from a water wheel, supplied the blasts of air at the furnace base.
Molten iron collected in the hearth. Meanwhile, impurities were coalesced by the flux into a slag, which floated on it. Workers would eventually break open the sides of the hearth (that were temporarily sealed with clay) and tapped the slag and iron. It was either cast in molds for utensils, kettles, or stove fronts or, more often, run in open, branched trenches where it solidified into "sows" and “pigs."
The refinery and chafery were housed in another building. In the refinery, workers melted the iron on a bed of glowing charcoal under blasts of air (allowing oxidation remove residual carbon). Workers then took this heavy, hot, and unwieldly mass (it is difficult to completely liquefy pure iron on a forge hearth) and lifted it out and worked and squeezed it under the power hammer into short, rough rectangular bars, called "blooms." They then took the blooms and reheated them in the chafery and shaped them into long wrought iron bars—the iron work’s main product.
Become a Member: How to Join ASME
In yet another building, workers took a portion of the iron bar and further refined it in a rolling mill. Parallel iron rolls driven by a water wheel with wooden pins for teeth reduced the reheated bar to flat strips, and workers took these and slit them into rods to make nails. The labor was difficult and “the workers had little protection beyond heavy leather gloves and aprons,” Murphy said.
Ending an era
A hidden secret of the site is that it hosts visitors picnicking, dog walking, or taking photos, Donovan said. In fact, the Commonwealth of Massachusetts boasts more wooded areas today than it had in the 1600s. And this was an issue for the early ironworkers. “They had to worry less about ore and gabbro running out and more about the trees for charcoal,” Murphy said.
“A ton of iron needed three tons of ore, two tons of gabbro, and 265 bushels of charcoal, and the Saugus blast furnace could produce six to seven tons of iron a week,” she explained. “There was no competition for the ore and gabbro, but the ironworks had to compete with the growing population of the colony and other industries for the wood to produce charcoal.”
Hammersmith wasn’t as long-lived as many of its successors. It wasn’t financially successful and seldom saw a profit. When the local bog ore became exhausted, importing resources was an expensive proposition. Meanwhile, foreign iron was getting cheaper. But despite the resource situation, “mismanagement of the iron works may have been the final situation that doomed the site,” Murphy speculated.
Read ASME's Landmark Description: Saugus Ironworks
Today, visitors enjoy “exploring the grounds and visiting the free museum at the park,” Donovan explained. “Inside the museum, you can see iron-making artifacts from the 1600s.” You can also find indigenous tools and colonial artifacts that illustrate how the Saugus River was used by diverse groups that have lived in the area over the years.
Cathy Cecere is membership content program manager.
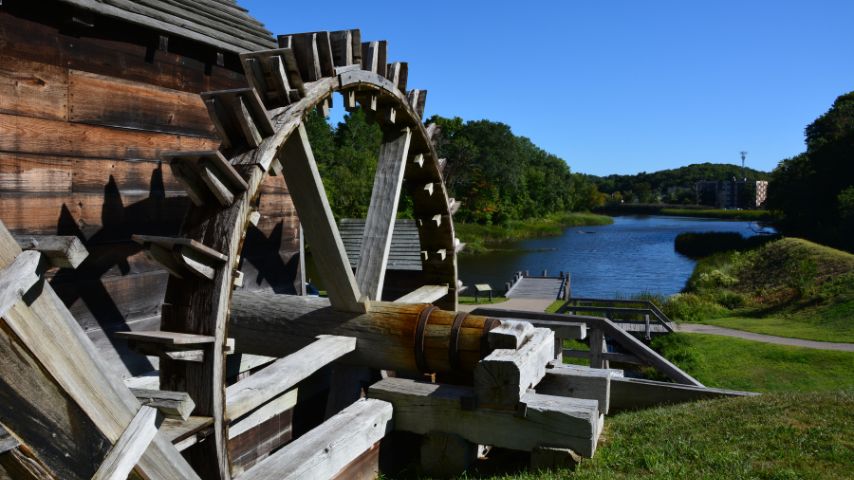
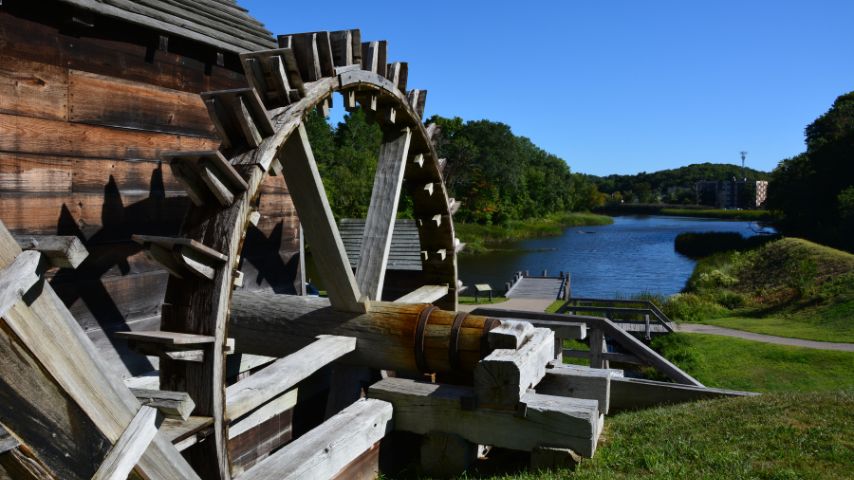